Common Faults and Troubleshooting Methods of Bridge Crane
Release time:
2022-01-24
1. The brake fails (the brake torque is small, and the lifting mechanism slips the hook). Slipping occurs in the operating mechanism. The reason analysis and its solution are described as follows. 1) There is oil on the surface of the brake wheel, and the friction coefficient decreases, resulting in a decrease in the braking torque, so the car cannot be braked. Kerosene or gasoline can be used to clean the surface oil can be solved.
Common faults of bridge cranes and their troubleshooting methods--
Common faults in mechanical transmission
1. The brake fails (the brake torque is small, and the lifting mechanism slips the hook). Slipping occurs in the operating mechanism. The reason analysis and its solution are described as follows.
1) There is oil on the surface of the brake wheel, and the friction coefficient decreases, resulting in a decrease in the braking torque, so the car cannot be braked. Kerosene or gasoline can be used to clean the surface oil can be solved.
2) The brake shoe lining is severely worn and the rivet is exposed. When braking, the rivet contacts the surface of the brake wheel, which not only reduces the braking torque but also damages the surface of the brake wheel, which is more harmful. Replace the brake shoe lining.
3) When the spring is improperly adjusted, the tension is small and the braking torque is reduced, and the car cannot be stopped, resulting in the phenomenon of rolling or hooking. Readjust the brake to increase its main spring tension.
4) The main spring is fatigued, the material is aging or cracks, no elasticity, and the tension is significantly reduced and the car cannot be stopped. The spring shall be replaced with a new one and adjusted.
5) Improper installation of the brake, the brake frame and the brake wheel are not concentric or skewed, resulting in hook slip or car slip phenomenon. Usually, first loosen the anchor bolts of the brake frame, then tighten the brake to make the brake shoe hold the brake wheel tightly, then fill the gap at the bottom of the suspended brake frame, and then tighten the anchor fixing bolts to achieve the two concentric.
6) Improper stroke adjustment of the electromagnet or support under the horizontal rod of the long-stroke brake electromagnet leads to failure to brake the car. Usually re-adjust the magnet stroke or remove the support can be solved.
7) The impeller of the hydraulic thruster is not flexible, resulting in reduced braking torque. Adjust the impeller to eliminate the jam resistance and make the impeller rotate and slide.
2. The brake cannot be opened
The reasons for the brake not to open and the elimination methods are as follows:
1) The tension of the main spring is too large, and the magnetic pulling force of the electromagnet is the tension of the main spring, so the brake cannot be opened. Readjust the brake, so that the main spring tension can be reduced.
2) The brake lever transmission system is stuck, and the brake release force is blocked in the transmission, so the brake cannot be opened. Check the transmission system and eliminate the jam phenomenon.
3) The brake screw rod of the brake is bent, and the head of the screw rod cannot touch the magnet moving iron core, so the brake shoe cannot be pushed away. Disassemble the brake, remove the screw and straighten it or replace the screw.
4) The brake lining rubber sticks to the working surface of the brake wheel with dirt. Remove the dirt on the surface of the brake wheel can be solved.
5) The electromagnet coil is burned or its wiring is broken, and the brake electromagnet has no magnetic pull. Replace the brake coil or connect the coil wiring.
6) The impeller of the hydraulic thruster is stuck. Clear the impeller jam fault.
7) The line voltage drop is too large, causing the brake electromagnet coil voltage to be lower than 80% of the rated voltage, and the magnetic magnetic tension is less than the tension of the main spring, so the brake cannot be opened. Clear the cause of the voltage drop and restore the normal voltage value to solve it.
3. When the brake is working, the brake lining heats up, "smokes", and has a burnt smell, and the lining wears quickly.
1) The gap between the brake lining and the brake wheel is improperly adjusted, the gap is too small, and the lining always contacts the working surface of the brake wheel during operation due to friction and heat generation. Re-adjust the gap between the lining and the brake wheel to make it uniform and completely disconnected during operation, and it is not enough to connect with the brake wheel.
2) The auxiliary spring of the short-stroke brake fails to push the brake shoe, so that the brake shoe always works on the surface of the brake wheel, which is caused by long-term friction and heat generation. Replace the secondary spring and readjust the brake.
3) The brake frame is not concentric with the brake wheel, and the edge of the brake shoe cannot be separated from the working surface of the brake wheel due to friction and heat generation. Reinstall the brake to achieve the concentricity requirement.
4) The working surface of the brake wheel is rough, the brake shoe lining is inconsistent with the brake wheel, and the brake is poor. Refinish the brake wheel or replace the brake wheel.
4. The braking torque of the brake is unstable
1) The out-of-roundness of the brake wheel is out of tolerance, the radial pulsation is large, and the periodic collision of the brake shoe during the braking process leads to the change of the braking torque. The brake wheel can be re-turned to meet the technical requirements or replace the qualified brake wheel.
2) The brake frame is not concentric with the brake wheel, and the brake wheel collides with the brake shoe during braking. Reinstall and adjust the brake carriage.
5. When the mechanism is running, the reducer vibrates on the bridge
1) The anchor bolts of the reducer base are loose and the fastening is not firm. Tighten the anchor bolt to fix it firmly.
2) The input shaft of the reducer is not concentric with the motor shaft or the output shaft of the reducer is not concentric with the driven workpiece shaft, which will cause the reducer to tremble during operation. Re-adjust the reducer to achieve the concentricity requirements to eliminate vibration.
3) The rigidity of the steel structure supported by the base of the reducer is poor, and deformation occurs during work and vibration occurs. It is sufficient to reinforce the support frame to improve its rigidity.
6. The trolley is in the "three legs" running state
The so-called three legs means that the car has three wheels in contact with the car track and one wheel is suspended. There are usually two situations:
1) There is always a car hanging in the air at any position of the bridge. The reasons and elimination methods are as follows:
① The gear manufacturing is unqualified, and the diameter is small beyond the tolerance range, so the gear is suspended under the condition that the frame installation axis is on the same horizontal plane.
Replace the gear to solve or adjust the installation position of the axle, so that it moves down to eliminate the phenomenon of suspension.
②The wheel diameters are all qualified, but the wheel installation accuracy is poor, the axes of the four wheels are not on the same horizontal plane, and the gear axes are high, so the phenomenon of suspension appears. Move the suspended wheel axle line down so that the four wheel axes are on the same horizontal plane.
③ The trolley frame is not manufactured to meet the requirements or is deformed, and the hanging angle will produce the phenomenon of "warping head. Correct the trolley frame, eliminate the warping phenomenon, and meet the qualified requirements can be completely solved.
2) The trolley has "three legs" in one or two or three positions of the bridge, and it is normal in other positions. The reasons for this are:
① The elevation difference between two main girders in the same section exceeds the allowable range, resulting in the suspension of the wheel above the main girder with the lower elevation.
② The installation quality of the trolley track is poor, and the elevation difference between the two tracks of the same section exceeds the allowable range. Usually, the trolley track is adjusted to make the top elevation of the two small rails of the section consistent or within the tolerance range.
7. Slip phenomenon occurs when the trolley is running
1) There are oil stains or sand grains on the top surface of the track, and frost in outdoor work.
2) The wheel installation quality is poor, and there is a suspension phenomenon, especially if the driving wheel is suspended or the wheel pressure is small. Adjust the installation position of the wheel and increase the driving wheel pressure.
3) The difference of the top elevation of the two small car rails in the same section is too large, resulting in too large difference of the driving wheel pressure. Adjust the trolley track to meet the installation standard.
8. When the car starts, the body sways and the vibration is serious.
When the running motor of the car is a squirrel cage motor, this phenomenon occurs when the driving wheel is unevenly pressed or a wheel is suspended due to its excessive start.
It can be solved by adjusting the wheel installation accuracy or adjusting the trolley track to meet the installation standard.
9. When the cart is running, the wheel flange gnaws the road (the wheel flange is severely worn, and sometimes even derails and falls off the road)
There are many reasons for the big car to gnaw the road.
1) The wheel is not qualified, especially the large difference in diameter between the two driving wheels, resulting in unequal linear speeds on both sides of the cart, causing the car body to skew. After measuring the diameter difference of the driving wheel, remove the larger wheel and retrain it to make it equal to the diameter of the other wheel, which can be solved after installation.
2) The transmission gap between the two sides of the transmission system is too large, causing the cart to be out of sync when starting, causing the car body to tilt and gnaw the rail. When braking, the gap difference is too large, which causes the car to tilt and causes the phenomenon of gnawing. Check the transmission system on both sides, eliminate the excessive gap, and make the transmission on both sides meet the technical requirements.
3) The installation accuracy of the wheel of the cart is poor, and the quality does not meet the technical requirements, especially the wheel tilts in the horizontal direction and guides the cart to walk obliquely, and the phenomenon of gnawing is extremely serious.
Check the installation accuracy of the measuring wheel, find out the wheel with horizontal deflection and readjust it to make the horizontal deviation less than L/1000(L-measuring chord length).
4) The bridge structure is deformed, causing the diagonal of the cart to be out of tolerance, causing rhombus to gnaw the cart wheels. Check and measure the relative difference between the diagonals of the two large vehicles, determine the correction direction, and usually use the flame correction method to correct the bridge frame, so that the diagonal tolerance of the large vehicle meets the technical requirements. Sometimes it is also possible to adjust the wheel position to achieve the relative difference of the diagonal of the cart to meet the technical standards.
5) Poor installation quality of the cart track, such as large elevation difference and span exceeding tolerance, will also cause the cart to gnaw the track and adjust the cart track to meet the installation standard.
6) When driving separately, the brakes at both ends are improperly adjusted, especially when one end of the brake is not safely opened, the resistance on both sides is inconsistent, causing the car body to walk obliquely and gnaw. Adjust the brakes at both ends so that they are fully opened during operation, and the braking torque at both ends is equal during braking.
7) The speed of the motors on both sides is different, resulting in different linear speeds on both sides. The motors should be replaced to achieve synchronization.
8) There are oil stains, frost, sundries, etc. on the top surface of the track, which is also one of the factors causing the cart to gnaw the track. Remove oil, frost, sundries, etc.
Key words:
Related Cases
220KV transformer tank full picture
2022-01-24
Full picture of 200KV transformer tank
2022-01-24
220KV transformer tank full picture
2022-01-24
ZHONGSHAN ABB TRANSFORMER CO., LTD
2022-01-24
220KV transformer tank full picture
2022-01-24
Share
Service Hotline
Telephone:+86-0757-87655338
Fax: +86-0757-87655330
Crane Division E-mail:ng@nangui.com.cn
Transformer Division E-mail:ngfueltank@163.com
Address: No.6 Jujin Road, Xincun Machinery and Plastic City, Baini Town, Sanshui District, Foshan City
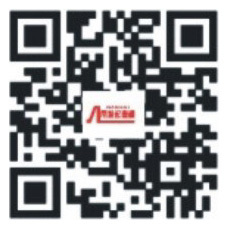
Sweep to learn more